In The News
Demystifying Systems Integrators & Automation Design Engineers
Which Approach Is Right for You: Systems Integrator or Automation Design Engineer?
When you’re partnering with a design firm to support your product development and manufacturing needs through automation. It’s important to decide whether you should work with a systems integrator or an automation design engineering firm.
In the first article of this three-part series, “Embracing the Power of Automation Design in Pharmaceutical Manufacturing”, we explored how automation helps pharmaceutical, biopharmaceutical, and biotech companies increase efficiencies and accelerate timelines for potentially life-saving therapies and technologies. Next, we will explore differences between how this support is provided by system integrators versus an automation design engineering firm.
Automation system design certainly requires consideration of several elements. Beyond the selection of a system platform, a good design engineer will work to understand their overall goals and objectives. Examples typically include improved reliability, increased automation (to reduce labor burden), redundancy, analytics, or greater integration between Building Automation (BAS) and Environmental Monitoring (EMS).1,2 The “how” in developing and executing this plan is significant, in order to best manage timeframe and costs for implementation of the plan.
What’s the difference between a systems integrator and an automation design engineer?
Simply stated, systems integrators are typically responsible for programming and implementing the automation system in a manner that conforms with the design requirement documents.3 Automation design engineers develop the design documents, while also focusing on how to best apply automation system changes in a way that is best aligned with a manufacturing process and overall facility purpose.4 This includes specifying designs that consider the owner’s plans for future expansions and upgrades.
To drill down a little deeper, the main role of systems integrator is to leverage software and hardware platforms, integrate them together into a single automation system, and implement the automation system itself. They specialize in hardware, software, and control systems, and their primary goal is to promote seamless communication and operation between various components of the automation system. They’re focused on technical aspects such as configuring the system, selecting and procuring the appropriate automation equipment, conducting testing and supporting validation of these systems, overseeing installation and commissioning, and providing ongoing support and troubleshooting.
Conversely, automation design engineers design, optimize, and improve the pharmaceutical manufacturing processes to ensure operational efficiency. They analyze existing processes, identify areas for enhancement, and prioritize productivity and product quality.4 Using 3D modeling tools and industry best practices, they predict process behavior, ensure compliance with safety and regulatory standards, perform process validation, and drive continuous improvement initiatives. Finally, they work with architects as well as mechanical, process, process utilities, electrical, and fire protection engineers to ensure that facility designs are fully coordinated with no design gaps.
Automation design engineers do not work in a vacuum. They collaborate with other engineers and systems integrators to define automation requirements based on identified process improvements and ensure alignment with overall process objectives.
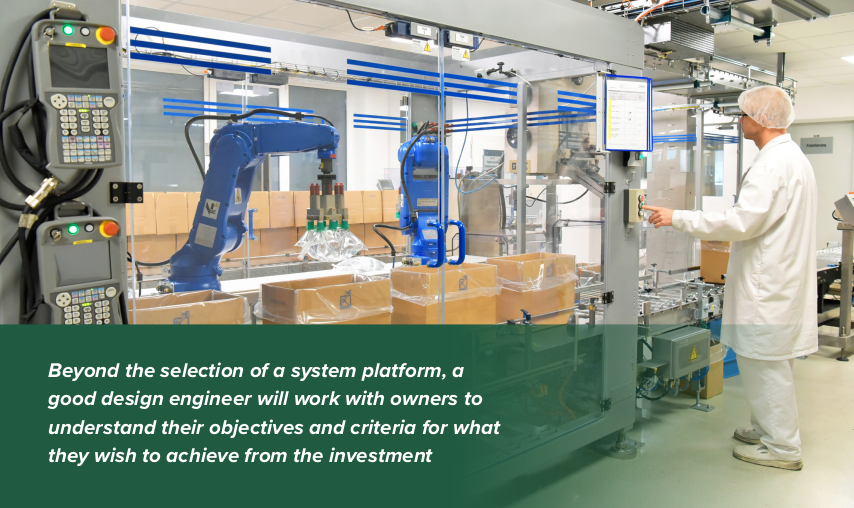
Beyond the selection of a system platform, a good design engineer will work with owners to understand their objectives and criteria for what they wish to achieve from the investment
The Value of Automation Design Engineers
Partnering with an automation design engineer can create the foundation for long-term efficiencies at reduced costs. These benefits include:
- Development of an Automation Master Plan that documents the overarching goals and criteria for upgrades of the facility and automation system, the parameters of the proposed system, anticipated costs, and timelines for system implementation.
- Development of necessary project documentation that pinpoints performance requirements for the automated system. Unlike many systems integrators who expect their clients to define the technical or process issue(s) that require their assistance, automation design engineers work with their customers. Once they fully understand the issue(s), they thoroughly review the current system(s), develop the automation solution, and guide the client through its execution.
- Assistance with bids to ensure the best solutions at the lowest price. By understanding what questions to ask, they can help the client avoid mistakes, delays, and cost overruns. This bid assist process also ensures the proposed system will best meet the objectives and criteria of the master plan.
- Experience and competency to oversee the integration and implementation of the automation system as well as a full understanding of how the system will function in totality with all manufacturing processes.
- Experience with the design and implementation of multiple automation systems and platforms. A system of checks and balances to ensure that all variables are considered and all business requirements are met.
Drilling Down into the Differences
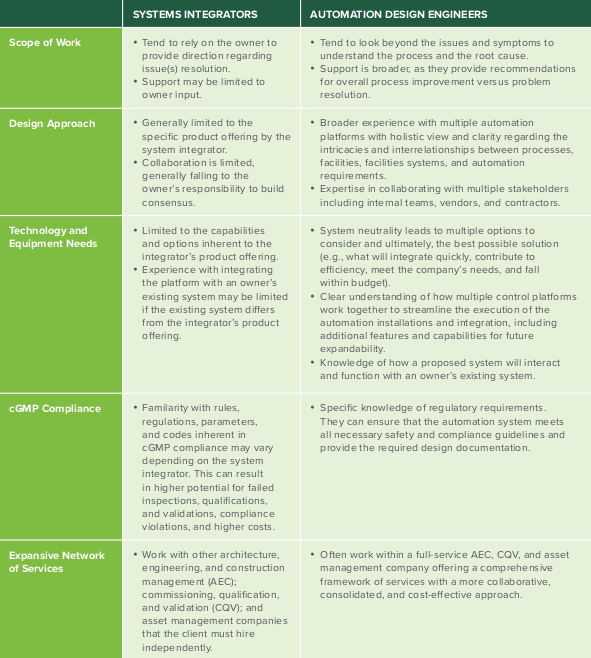
SYSTEMS INTEGRATORS | AUTOMATION DESIGN ENGINEERS | |
Scope of Work |
|
|
Design Approach |
|
|
Technology and Equipment Needs |
|
|
cGMP Compliance |
|
|
Expansive Network of Services |
|
|
Choosing the Right Partner for Your Automation Needs
Whether you hire a systems integrator or an automation design engineer, you need to evaluate your needs. Given these points, below are some questions to ask:
- Does the firm have strong experience, particularly within the life sciences industry and with cGMP requirements?
- What is the firm’s expertise, and specifically that of the personnel executing the work?
- What overall level of customer service do you need? How responsive should your partner be?
- Does the firm provide automation design services in-house, or will you need to outsource those services?
- If I do need to outsource services, how do I ensure that all parties work together seamlessly and prevent gaps in the design?
- Will the firm’s automation approach be forward thinking (e.g., aid in developing new products/expanding future manufacturing capacity)?
- Does the firm have the industry experience with various automation platforms to choose the right solution for my facility?
- Does the firm have experience throughout the project lifecycle—from planning and design to oversight and validation?
- Is the firm able to consider potential site-wide impacts to the whole plant?
- Does the firm have the design experience to integrate different platforms into a single solution?
- Will the firm be able to ensure that the design meets all facility requirements and needs?
While systems integrators are essential in implementing the technical aspects of the automation system, an automation design engineer can ensure your project aligns with your business objectives, regulatory requirements, goals for operational efficiency, future growth, and cost containment/ROI.